Tile cutting business upgrades their waterjet system
after 20 years of operation

TILE
Reduce programming time
Increase profit margin
Extend customer base and secure larger contracts
Improved ease of operation, machine capabilities, flexibility and cut quality
Doubled productivity and backup system
Industry of Reference and Business Model
N & Sons Tile Cutting is a family owned and operated business with a combined 20 years of experience. They have an experienced team that takes pride in creating highly accurate and stunning tile cuts to enhance kitchens, bathrooms and outdoor areas using products from only the best brands.
Their success resides in quality workmanship and attention to detail.
Keep innovating and don’t get left behind
Now, 20 years later, they upgraded to a new Intec™G2 35 (1 x 1.5 meter).
Mira stated:
“With 20 years of continuous and reliable operation with first class local support,
it was a decision that required no analysis.
Also, that waterjet technology enables less material handling therefore saving time.
There is no need for external CNC work, waterjet does it all.”
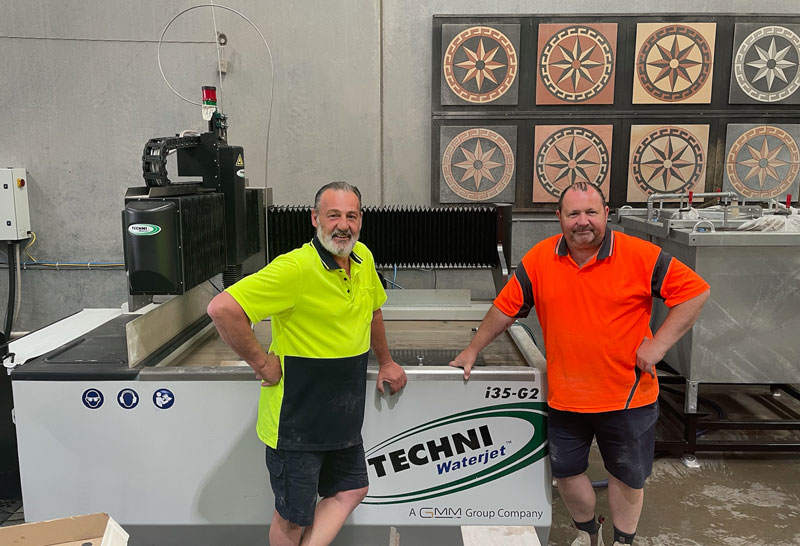
What Prompted N & Sons to Return to Techni for Their Second Waterjet
Techni Waterjet is a global company that has been around for 32 years. It has sold more than 1500 waterjets worldwide in that time.
With investments in high-quality service technicians holding more than 20 years’ experience and knowing Techni was the manufacturer of the entire waterjet system, including software, the brothers were confident they were making the right choice.
The long-term, successful relationship between Techni and N & Sons was also a key factor in their decision to invest in a second Techni system.
Mira stated:
“We knew upgrading to another Techni Waterjet cutter was the right choice because of the successful long-term relationship we already had in place, and their ongoing technological innovations.
A major difference between the systems was the software!
We were amazed at the simplicity and efficiency of it.
It’s a clean, user-friendly interface that has a lot more flexibility than what we were used to.”

Real Benefits and Peace of Mind
Sales Director at Techni Waterjet, Glenn Langdon further discusses the benefits of the Softec™ software.
“Our waterjet cutting technology was developed by our team of engineers with two very clear goals in mind. The first was to give workshops the intelligence to cut parts at a minimum cost. The second was to be able to have users control it from an all-in-one interface.
In developing this software, we wanted to ensure the software’s ease of use.
From novice to advanced levels, you can easily gain the most out of your waterjet cutting machine with Softec software.”
The software incorporates a 3 simple step process.
Step 1 – Select your CAD file and the material that you will be cutting. The software will then automatically load the pre-defined settings to cut this material type.
Step 2 – Input the dimensions of the material thickness, length, and width of the sheet to be cut.
Step 3 – Confirm your machine’s configuration and press go. Your machine will do the rest.
This simple process has enabled N & Sons as well as many other customers to operate in a fast and easy way.
Also, thanks to proprietary Softec NEST™ nesting software, Techni demonstrated how the machine could have allowed N & Sons to nest more parts per sheet and reduce programming time, saving them thousands of dollars per year. The nesting software utilizes advanced nesting algorithms developed by Geometric Global which is specifically developed to maximize production while leaving minimum scrap material.
